Underwater Remote Mining
Underwater remote mining (URM) is a potential technological breakthrough for kimberlite diamond mining. A new innovative solution which originated from deep sea mining and trenching systems, it has allowed Burgundy and Dutch company Royal IHC Mining to take the next step in the future of kimberlite mining. Ekati and Royal IHC Mining, a supplier of maritime technology, started working together in 2018 to jointly develop this innovative and integrated mining technology.
The starting point for the development of the URM system was to economically extract kimberlite from marginal kimberlite pipes and from deeper portions of completed open pits at Ekati. An important focus was to develop a mining solution that would have a much lower environmental impact than conventional mining methods. As the URM crawler is only mining the kimberlite ore and minimal waste, it significantly reduces the mine’s footprint, in addition to lowering the operating costs. The URM solution could allow the Ekati Diamond Mines to extend its lifetime as an alternative to conventional mining recovery techniques.
The Underwater Remote Mining System
The underwater mining crawler is a remote operated continuous mining machine, equipped with the latest underwater control and positioning equipment. It consists of four tracks with independent suspension and steering, a centrally placed drum cutter, an ancillary cutter for kimberlite along pipe contacts, a high efficiency dredge pump and submerged hydraulics with biodegradable oil.
The ore is directly excavated with a drum cutter in small layers and eliminates the need for blasting explosives. From the crawler the ore is pumped to the surface of the flooded open pit via a vertical pipeline system to the launch and recovery platform, from which the ore is transported to a dewatering plant. The dewatering plant and slurry lines will be constructed and commissioned on site at Ekati. The crawler system is capable of operating at a water depth of up to 400 meters and will be operated remotely from a control room at the edge of the open pit. Pictured below is a conceptual rendition of the mining crawler.
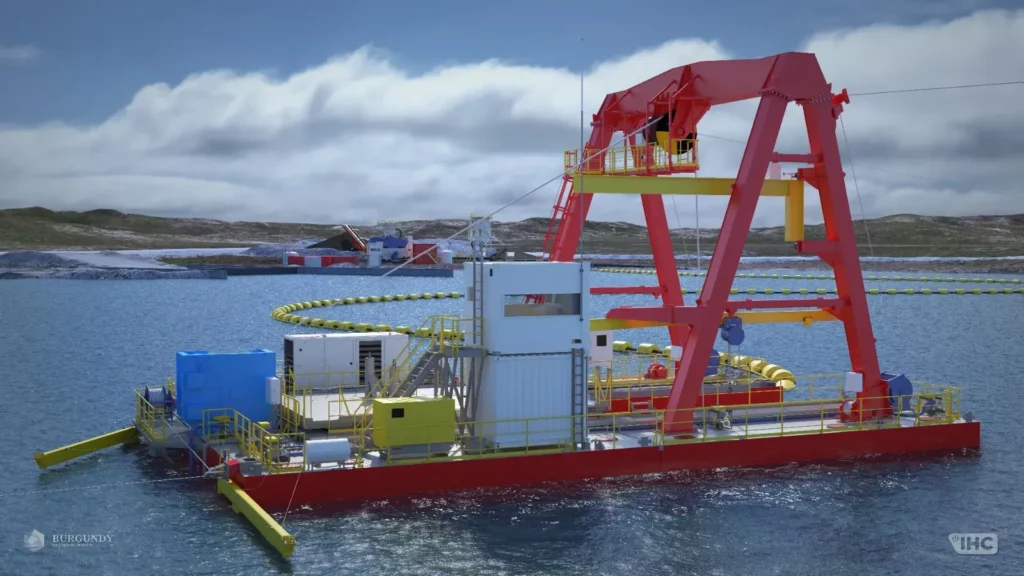
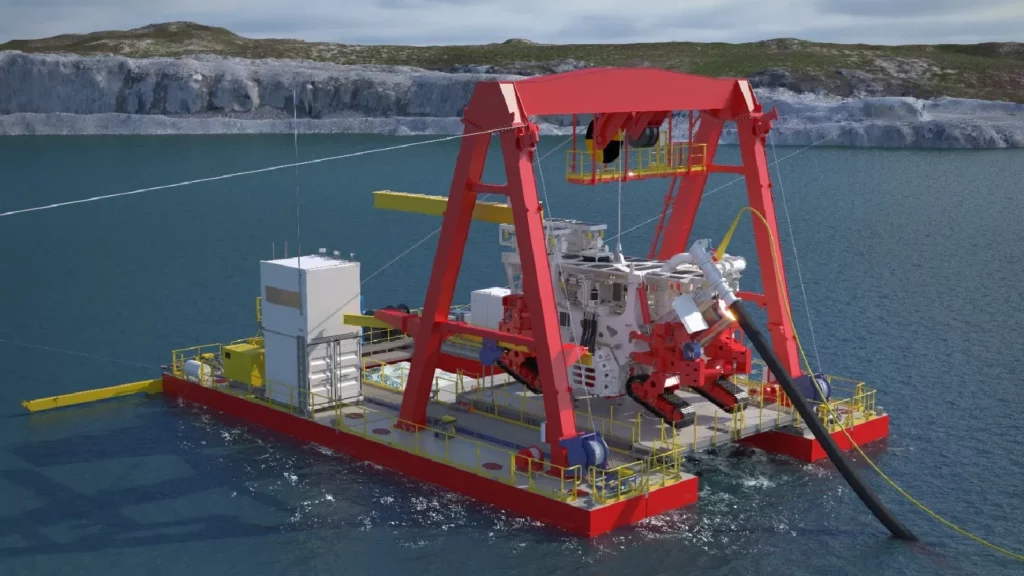
The Underwater Mining Crawler
The underwater mining crawler is a remote operated continuous mining machine, equipped with the latest underwater control and positioning equipment. It consists of four tracks with independent suspension and steering, a centrally placed drum cutter, an ancillary cutter for kimberlite along pipe contacts, a high efficiency dredge pump and submerged hydraulics with biodegradable oil.
The ore is directly excavated with a drum cutter in small layers and eliminates the need for blasting explosives. From the crawler the ore is pumped to the surface of the flooded pit via a vertical pipeline system to the launch and recovery platform, from where the ore is transported further to a dewatering plant. The dewatering plant and slurry lines will be constructed and commissioned on site at Ekati mine . The crawler system is capable of operating at a water depth of up to 400 meters and will be operated remotely from a control room at the edge of the pit. Below are conceptual renderings of the mining crawler, along with a group photo featuring the Burgundy Crawler taken in August 2024. Photo credit: IHC Mining/Royal IHC.
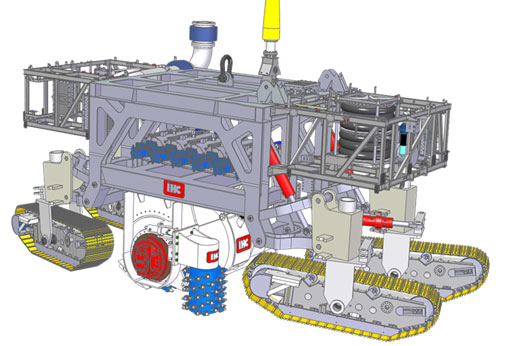
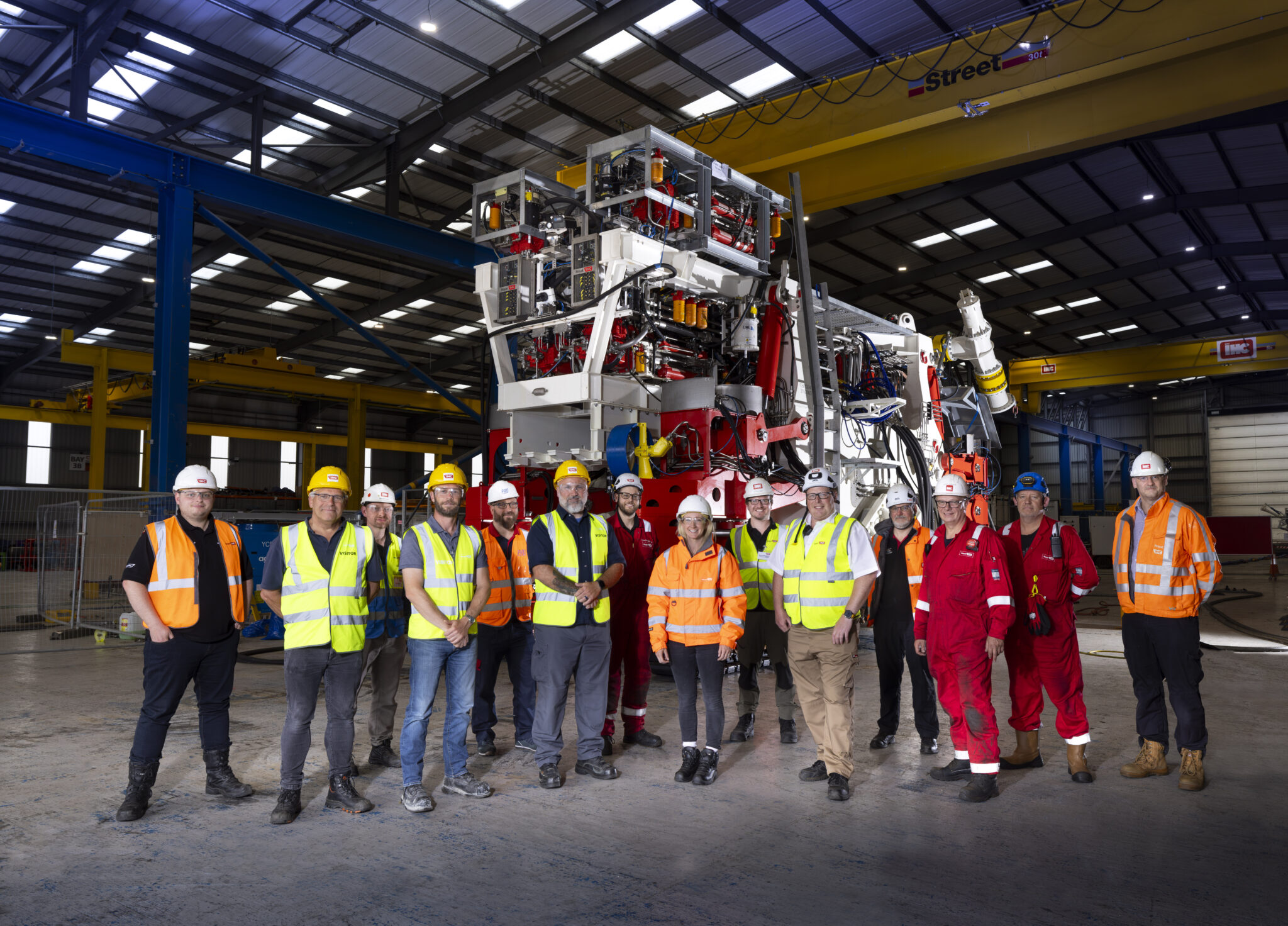
URM Testing
The Lynx open pit was successfully flooded in summer 2023, marking the first phase of the URM system testing. In August 2024, a team from Burgundy traveled to the UK to complete the Factory Assurance Test for the crawler. The next phase will involve testing the launch and recovery platform in summer 2025, followed by comprehensive testing of the full URM system in summer 2026. This final phase will include a trial mining operation, targeting the extraction of approximately 180,000 tonnes of Lynx kimberlite ore. Below is a conceptual aerial view of the future URM setup and trial at Ekati’s Lynx open pit.
The URM method could be a technological breakthrough for kimberlite diamond mining and a sustainable future alternative to conventional mining methods. URM technology has a much lower environmental impact, significantly reducing Ekati’s mining footprint.
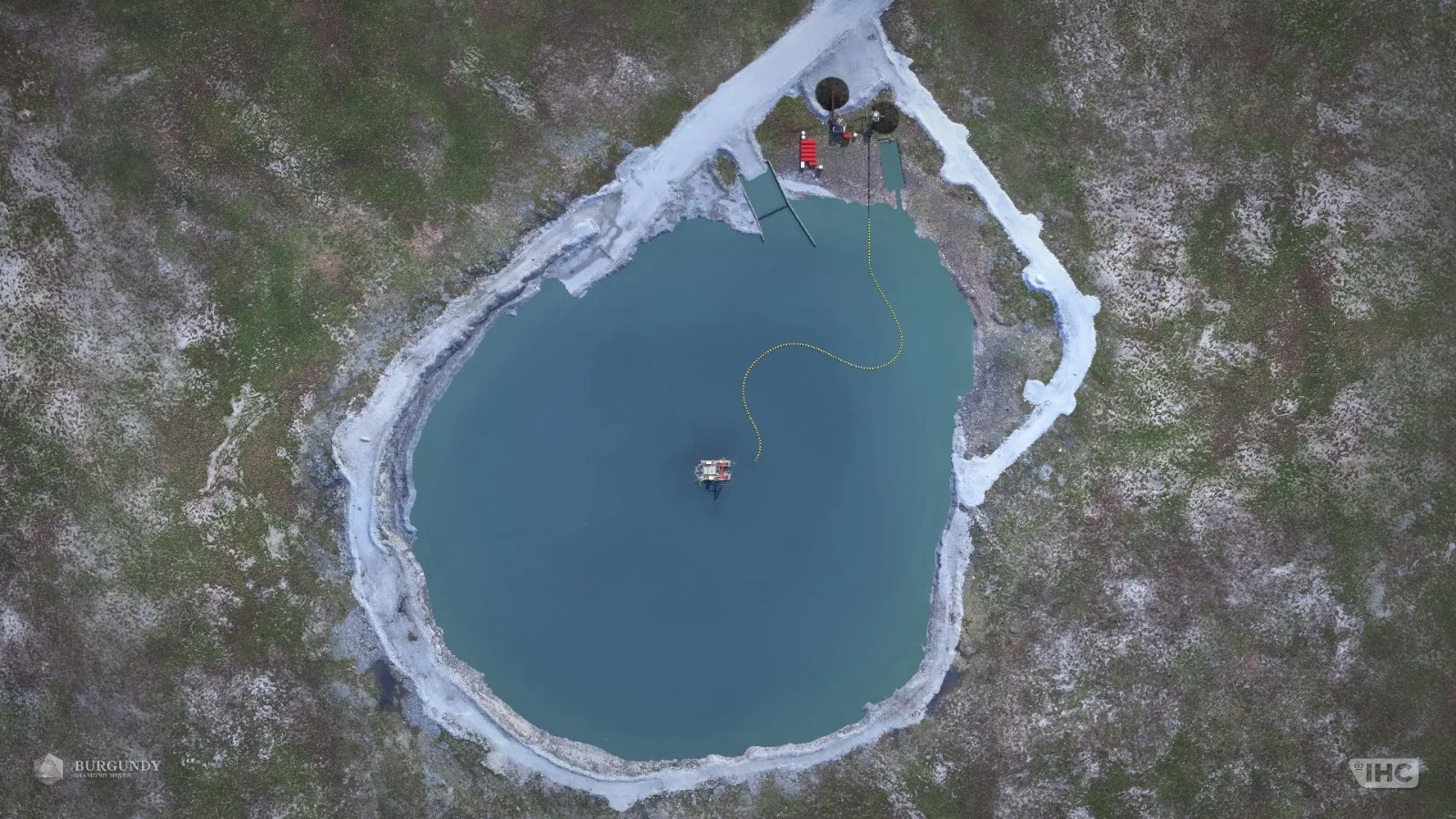
The URM solution is a technological breakthrough for kimberlite diamond mining and a sustainable future alternative to conventional mining methods. URM technology has a much lower environmental impact, significantly reducing Ekati’s mining footprint.